Do you have questions about the WMT?
Shell construction with the WMT
3 employees plus 1 crane driver manufacture 20 walls per week!
Precast concrete walls
Wall production mobile and flexible
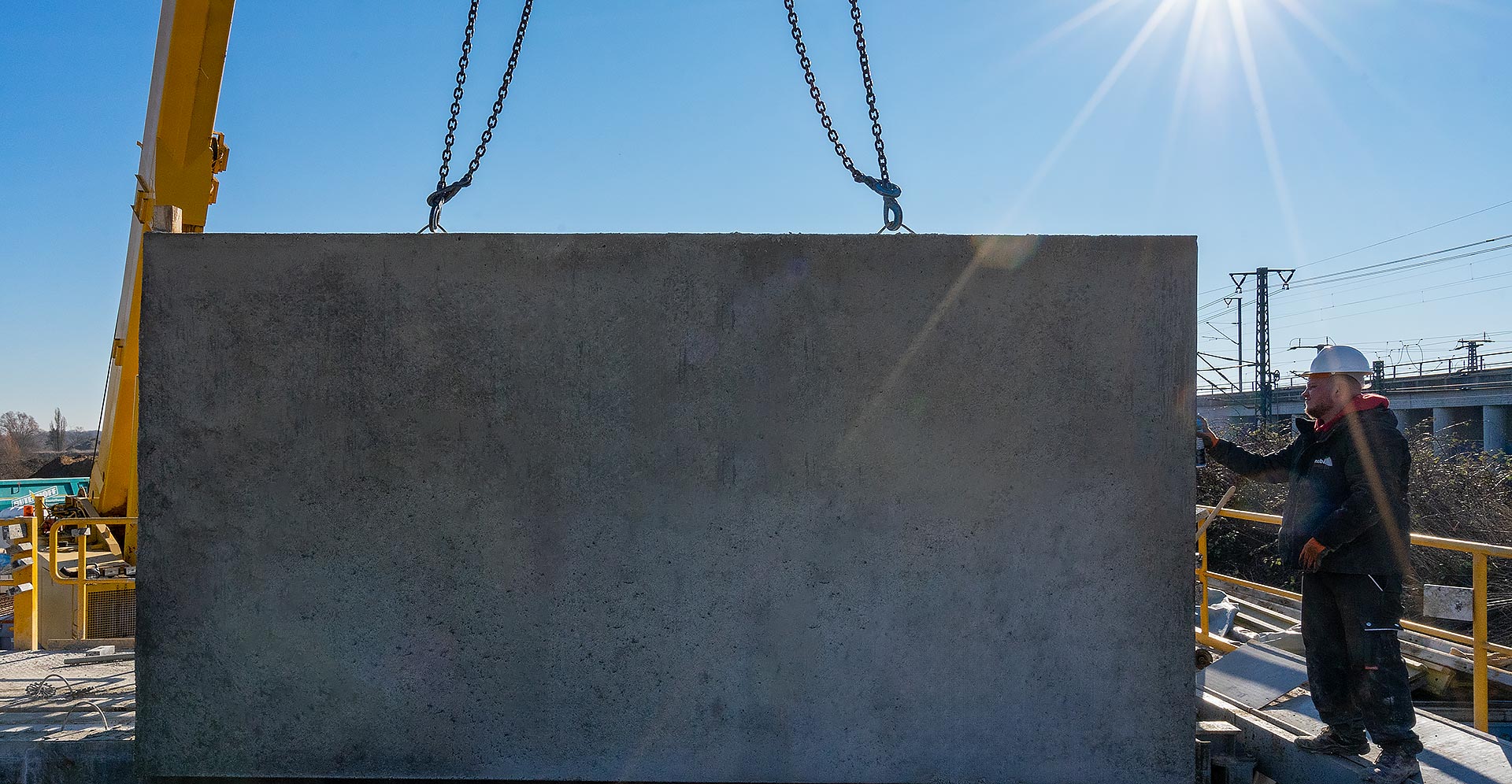
Wall production process
For wall production, the “toaster” requires a floor area of approx. 150m² plus space for office and crew containers. Area for office and crew containers.
The entire production process incl. Assembly and disassembly can be realized by three workers plus a crane operator.
- Foundation concreting
- Assambly: 3 days (WMT M7)
- Set-up (formwork, wall thickness, etc.) for 10 walls: 8-10 hours
- Concreting: 3 hours
- Drying time: depending on outside temperature and/or optional heater
- Pulling walls: 3 – 3.5 hours
- Disassembly: 3 days (WMT M7)
Process of the shell construction
Due to the prefabrication of the concrete walls on site, up to 12 walls per day can be installed by 3 employees plus 1 crane driver*.
- Preparation of the settling place for the prefabricated wall by means of a mortar relining or rim stones.
- Picking up the wall to be installed by the construction crane
- Lifting the finished wall from the WMT
- Setting down the wall at the intended position
- Aligning the wall with the position
- Securing the wall with two support columns
- Connecting the wall with the previously installed prefabricated wall
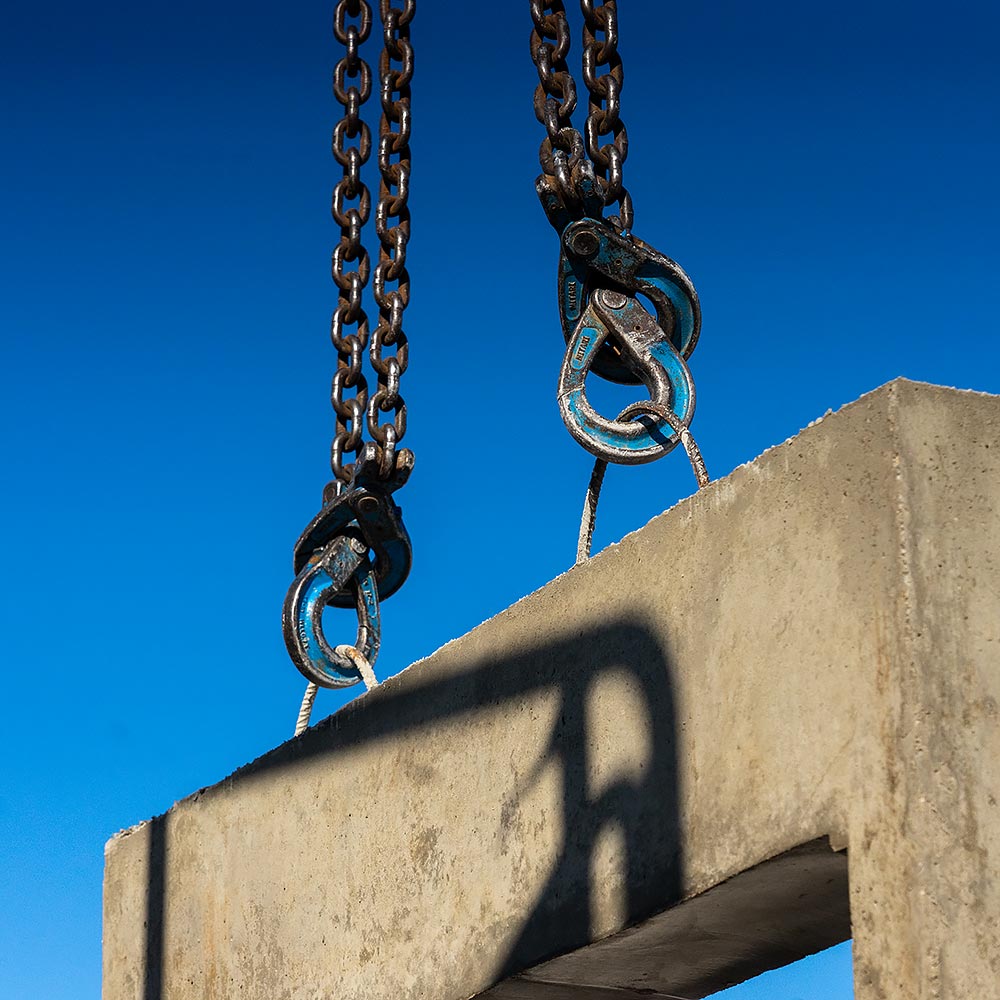
20 walls per week!
flexible wall thicknesses from 6 - 20 cm (please ask for thicker ones)
Concrete walls up to 8 m long and 2.70 m high
WMT available in two sizes
Assembly of the Wall module toaster in video
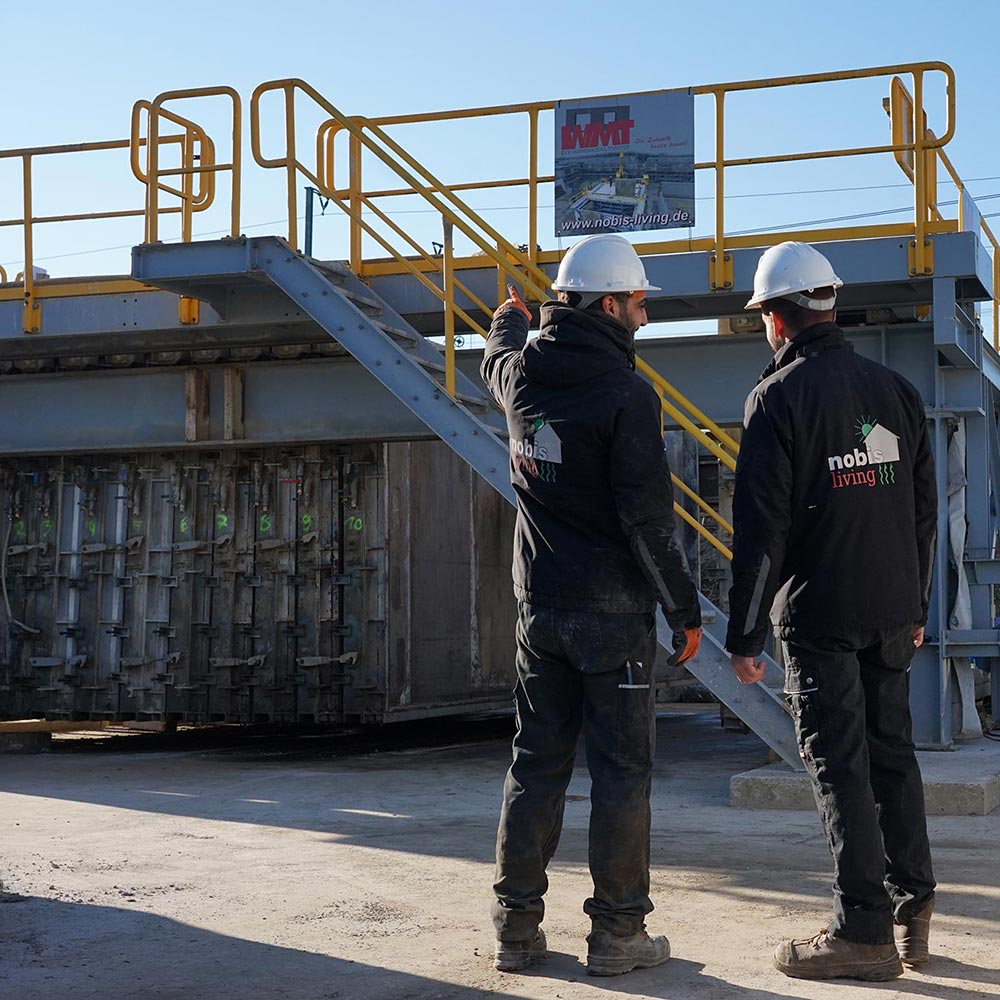
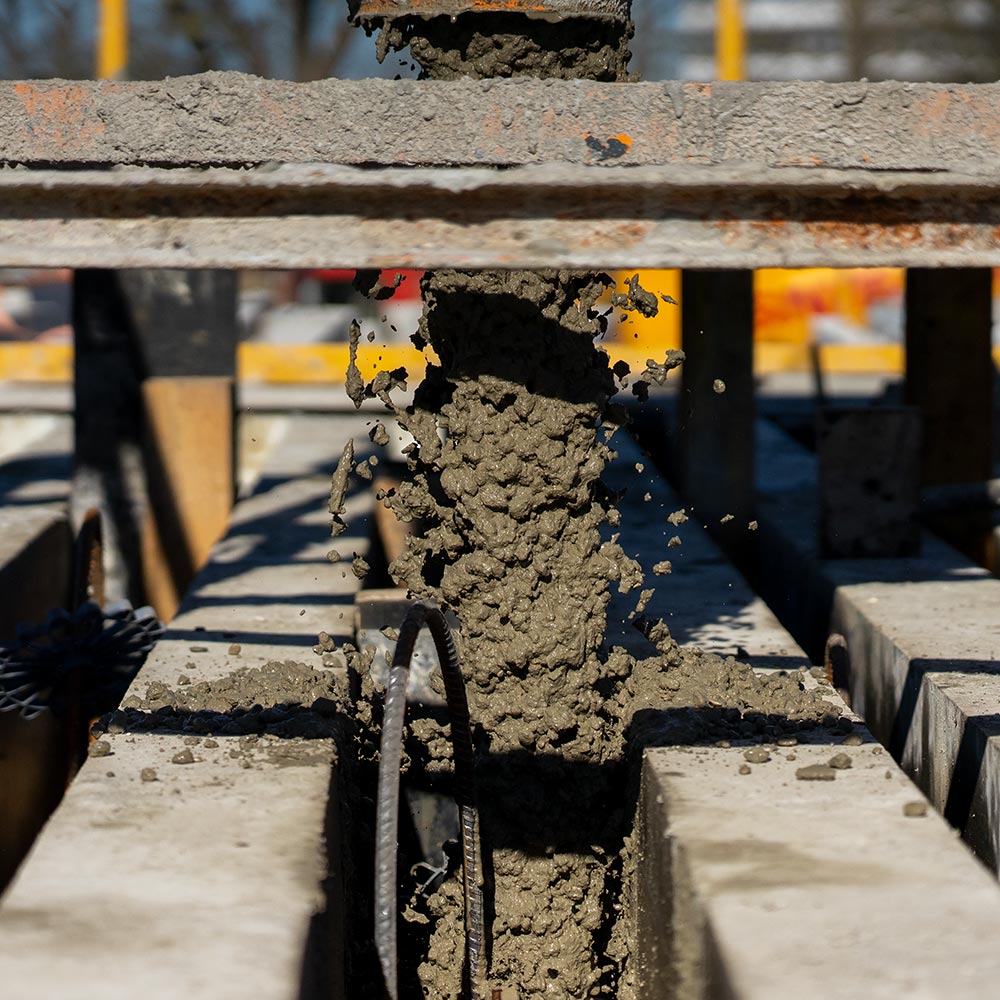
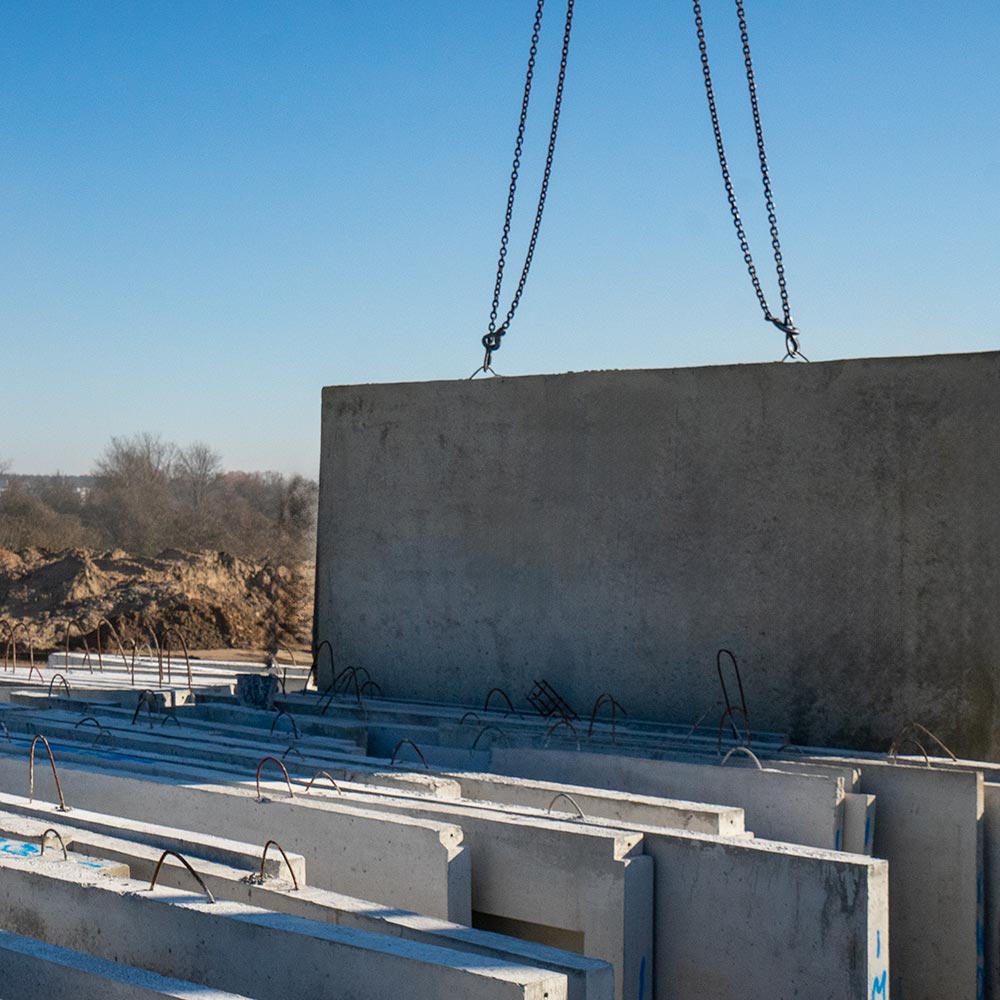
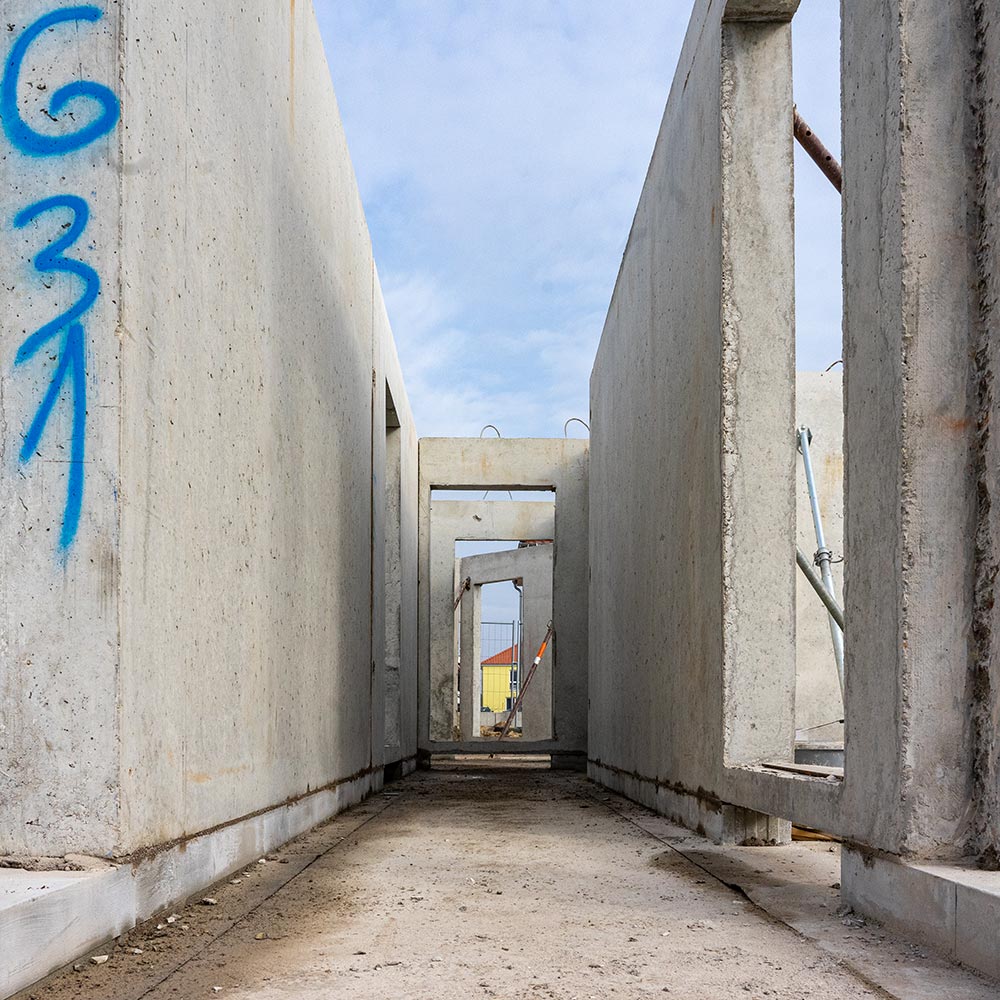
F.A.Q.
Frequently Asked Questions
How many trucks are needed to transport the WMT?
The mobile wall module toaster can be transported with five truck loads (WMT M7), the larger M8 has six loads.
What is the energy requirement during the toasting process?
Since the toaster is operated purely mechanically, no energy is required other than a few machine tools (impact wrench, binding machine, internal vibrator).
Can I get funding for the purchase of the WMT?
Yes, you can receive a subsidy of up to 40% of the purchase costs under the BAFA subsidy program.
Ceilings
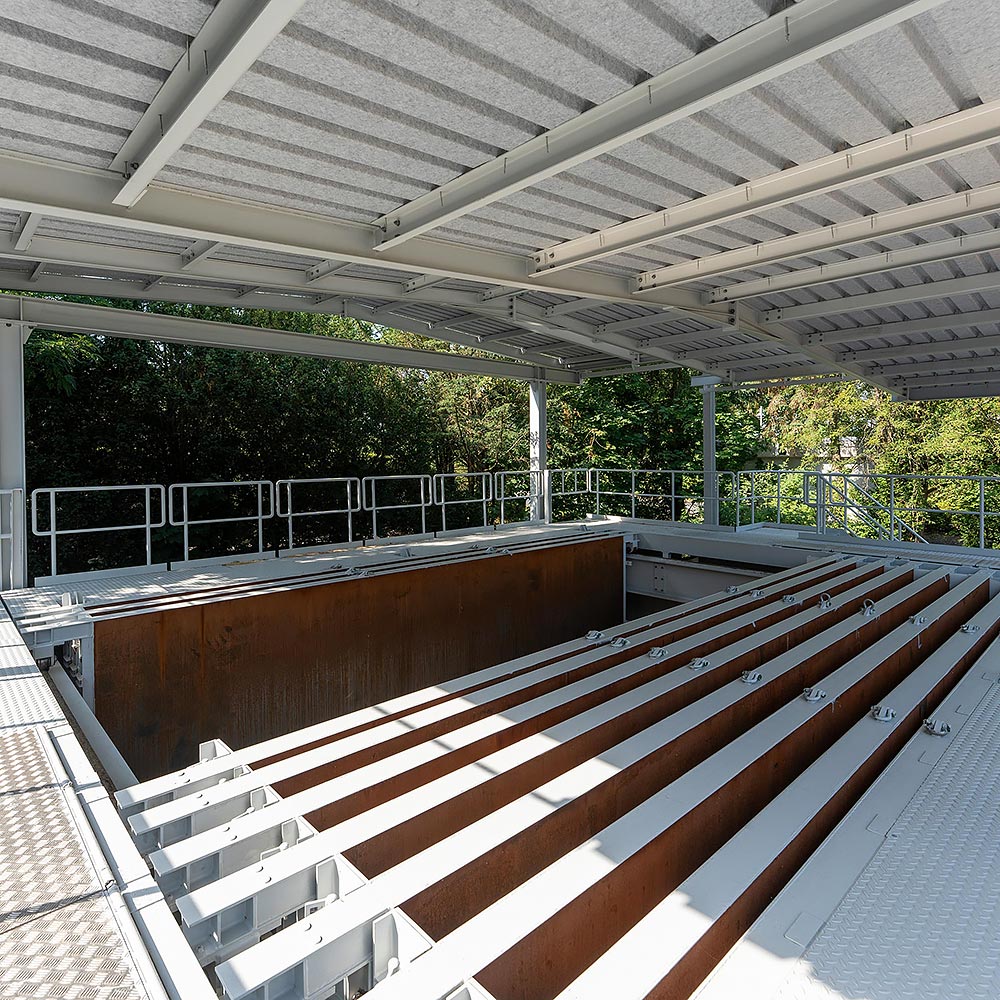
Filigree slabs or hollow core slabs?
We recommend the use of hollow core slabs, which in our opinion have many advantages
- The parallel production of the ceilings at the manufacturer shortens the shell construction time
- Reduced material requirements and lower dead weight, only approx. 50% concrete, 75% less steel, resulting in a reduction of loads in the building
- Very high load capacities
- No load-bearing interior walls necessary
- Delivery directly to the construction site, at the specified time
- Assembly takes place directly from the truck
- An assembly team consists of only max. four employees and creates up to 400m² of ceiling space per day
- Supporting the slabs is no longer necessary, which results in further material savings and speed advantages
Contact us
Send us a message using the small form below or feel free to call.
Phone
+49 (0)5102 675 4373
Office
Bremer Str. 9 • 30880 Laatzen • Germany
Opening hours
Mo. - Fr. 08:00 - 17:00