Advantages of the WMT
With the help of the WMT (wall module toaster), you can also realize larger shell constructions with approx. 10 employees, e.g. facilities for assisted living, student housing, commercial properties, or multi-family houses.
Wall manufacturing with only 3 employees
20 walls per week
365 days a year
Walls smooth with formwork on both sides
A toaster on the construction site
Serial construction with the WMT has many advantages
Mobility
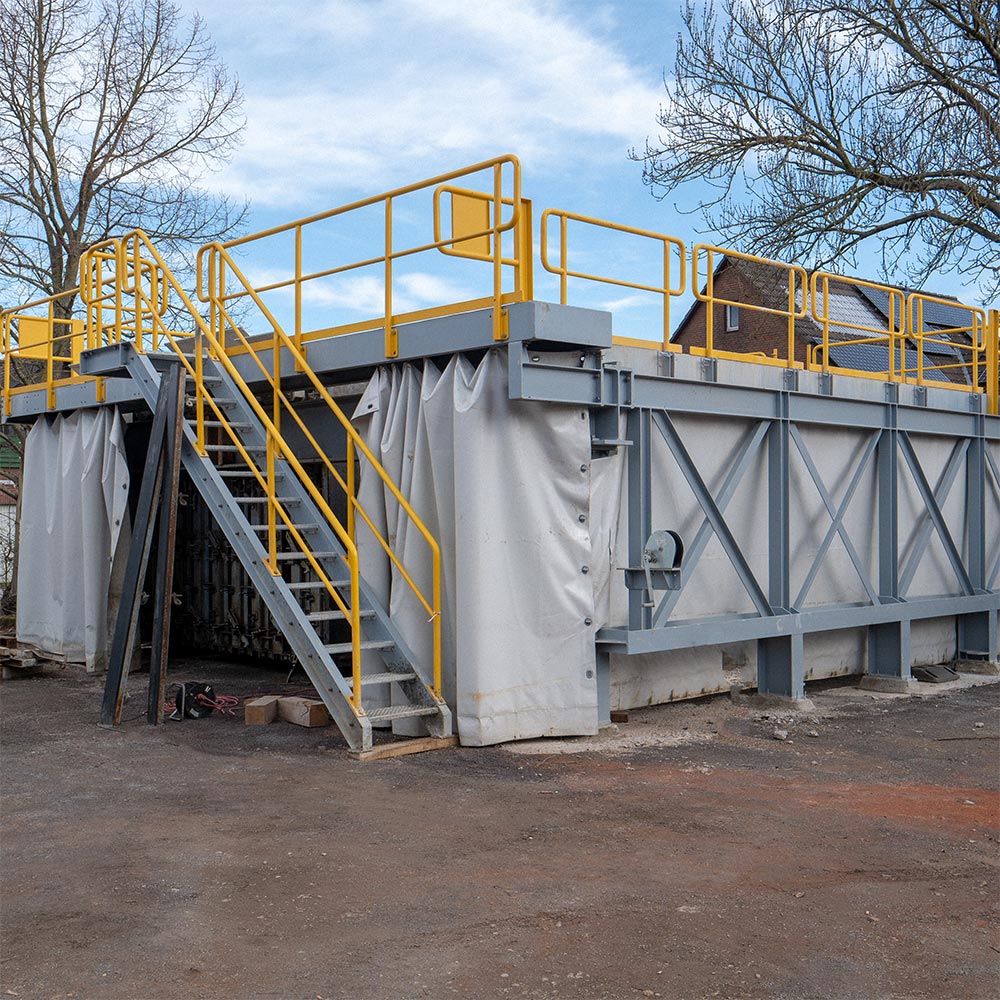
Infrastructure problems such as dilapidated bridges and roads are leading to ever greater challenges in the transportation sector. Congestion and detour significantly affect the availability of materials and products on time. The consequences are delays in construction. The Wall modul toaster produces your precast walls directly on your construction site. The concrete needed to make your walls is always available nearby, delivery times should no longer be a problem.
- You have your WMT Wall modul toaster directly on your construction site
- You have your own produced walls immediately available without transport logistics
- Only few transports needed to move your factory
- No need for long journeys for ordered prefabricated walls/modules from the factory = time savings
- A concrete supplier is nearby = short distances
speed
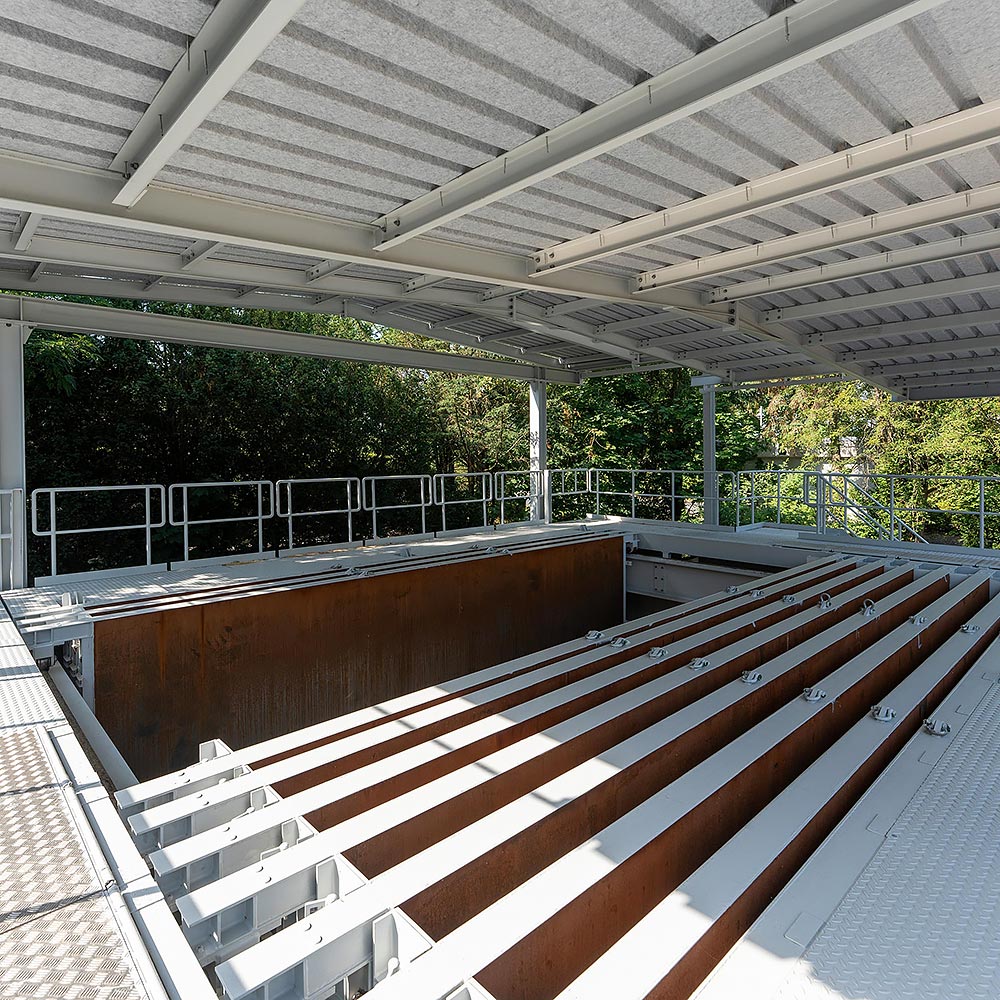
The construction speed is an important item in the calculation. If the shell is finished faster, the money is more likely to flow. However, quality must not fall by the wayside. The WMT produces formwork-smooth walls on both sides that can be processed directly. Optional components like roof and heating make you less dependent on the weather and can produce more concrete walls.
- 10 walls can be produced at the same time
- High wall quality, formwork smooth walls on both sides
- Year round production possible
- Easier construction site management
Flexibility
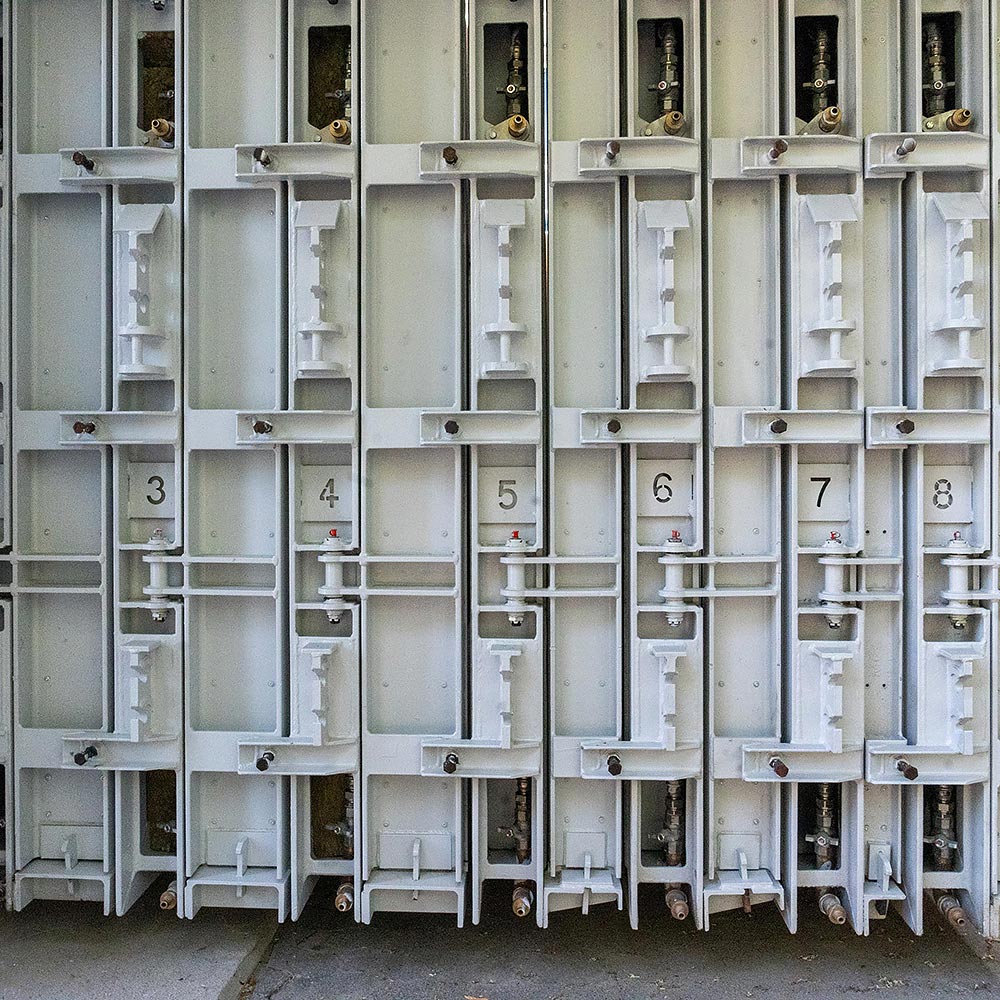
In contrast to ordered walls from the precast plant, you are much more flexible with your own wall production. If changes occur in the shell construction, you can react quickly with the WMT and its planning software. In addition, the machine produces walls with different wall thicknesses in one pass.
- Changes in the construction process are possible at any time. The planning of the walls to be changed can be implemented directly on site by you.
- Different wall thicknesses between 6 and 20 cm (approx. 2,36 – 7.86″) can be produced simultaneously.
- Your shell construction does not come to a standstill, your team has hardly any downtime
Professionals
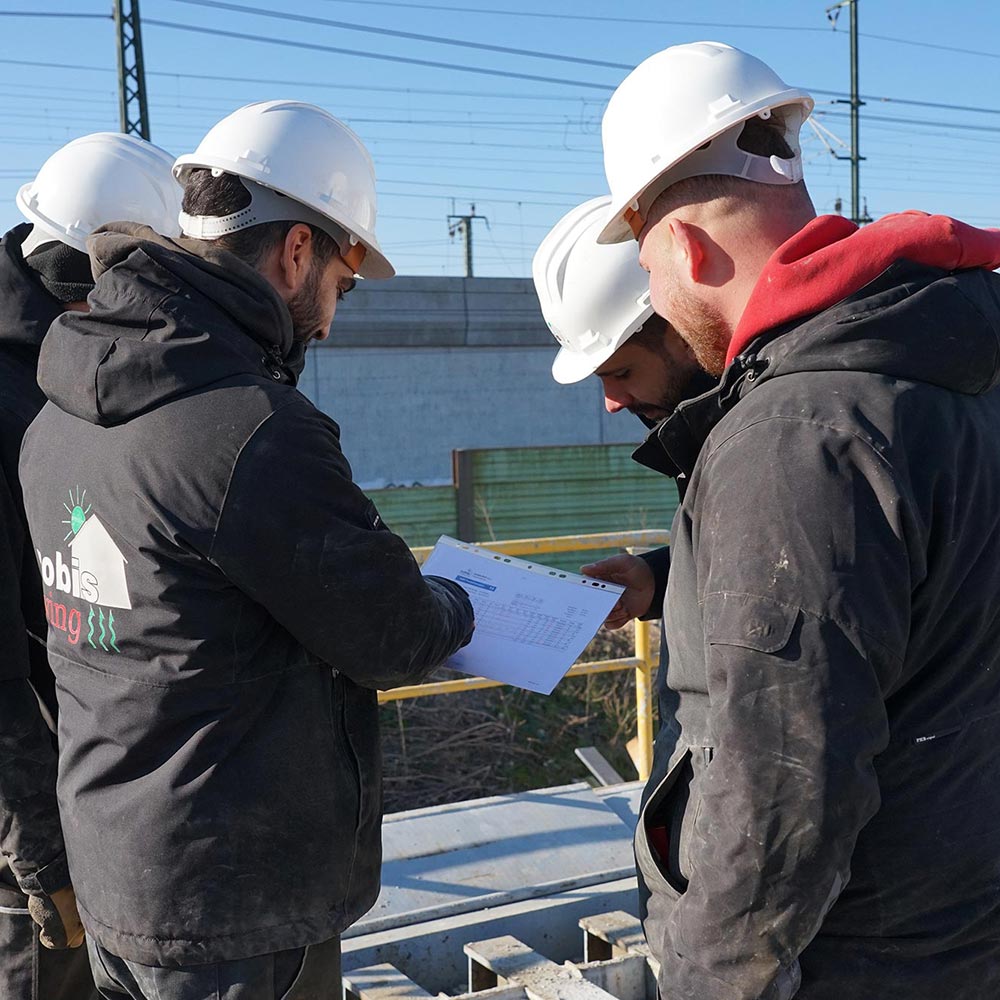
Invest in machine technology and respond to the shortage of skilled workers. The WMT only needs 3 people for wall production. With a further 7 employees, you can also implement the shell construction of larger properties such as nursing homes or student housings with over 100 residential units. The operation of the WMT is easy to learn. The physical effort is less than in the conventional construction method.
- Higher productivity
- Also larger shell constructions with max. 7 people possible
- Smaller number of employees required
- Less physical strain, less bending / lifting
Maintenance
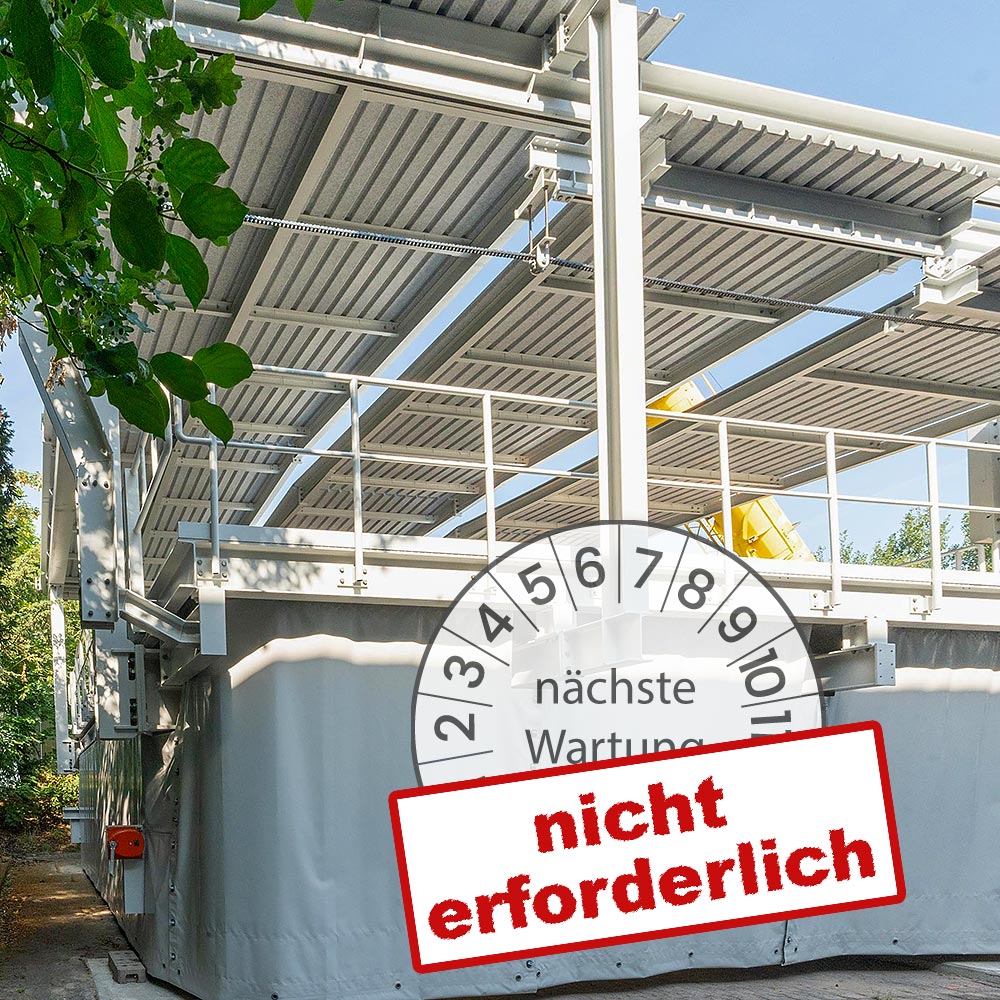
No maintenance = no downtime!
The maintenance of the machines is a necessary, yet annoying evil. No contractor likes the downtime involved. Since the WMT (wall module toaster) is a purely mechanical solution, no maintenance is required in wall production. The WMT requires a little maintenance for smooth operation: after each removal of the concrete walls, the chamber walls must be protected with formwork oil. In the optional heater for winter use (at +5°C or less), a heat pump is used to pump a heat transfer medium through the chamber walls. This allows your WMT to supply concrete walls to well over 1,000 job sites!
- purely mechanical solution
- No maintenance required
- Only little care required during operation
- No hydraulics available
- no electricity needed for operation (except in winter)
Planning
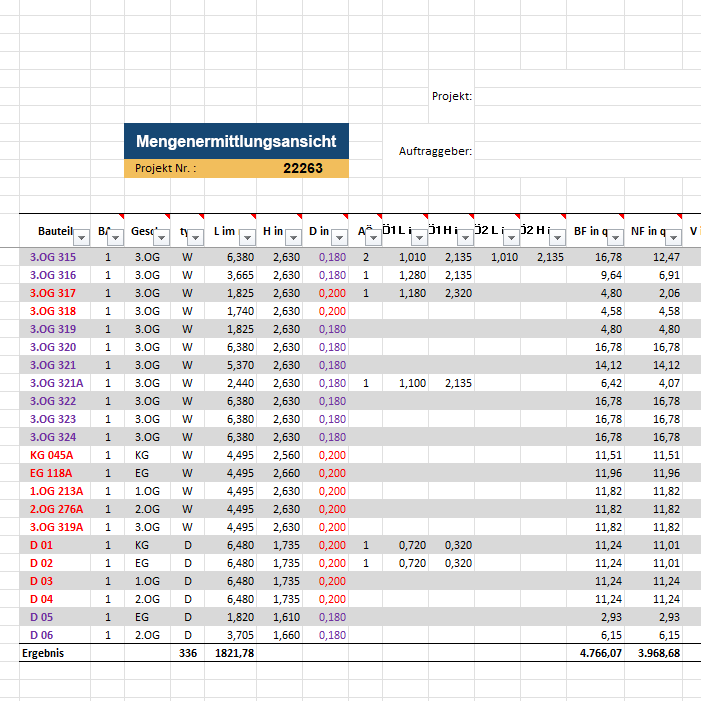
The nobis living group of companies has been building with the WMT in serial construction for several years. In order to better organize and optimize construction processes, we have developed a planning and logistics software to go with the WMT: One planner can control up to four “toasters” with this program.
- Production schedule
- Shell construction material determination
- Production lists
- Cost center directory for accounting
- Production overview
Construction of a residential complex for assisted living in Pattensen
with the first WMT in 2017
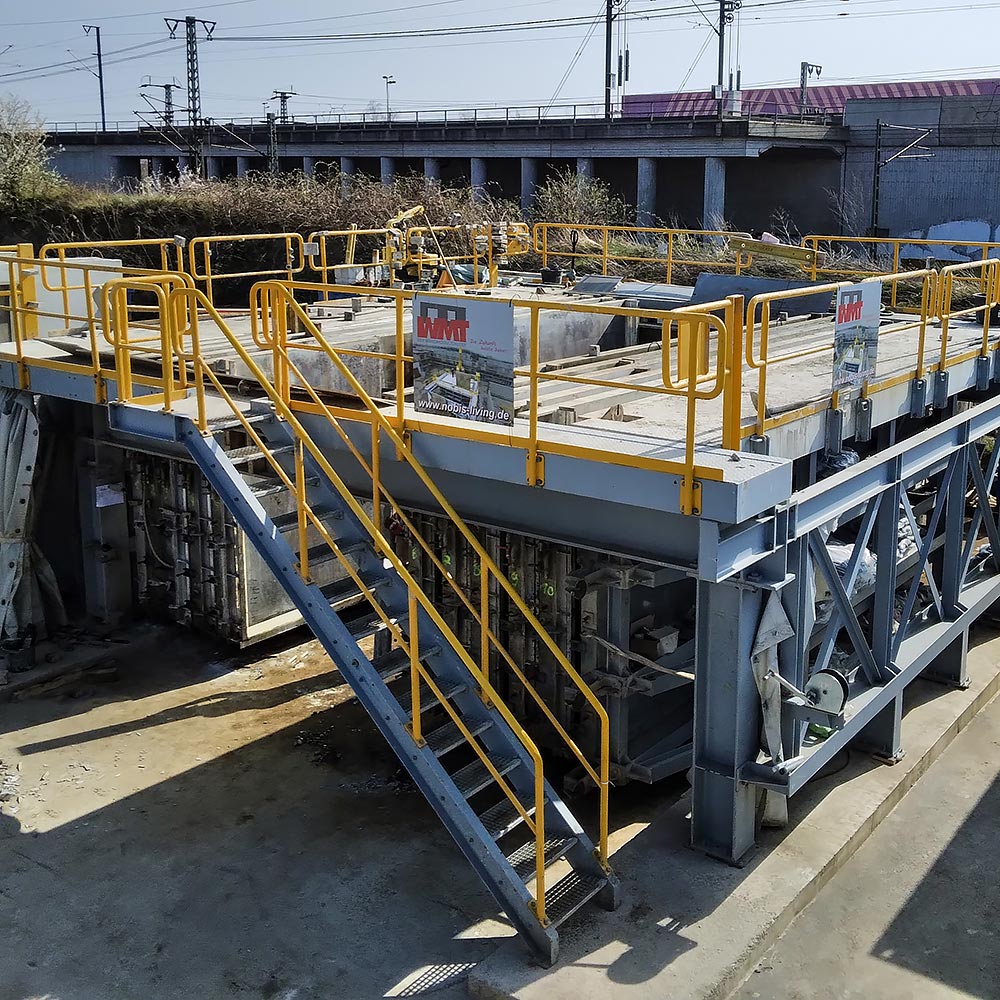
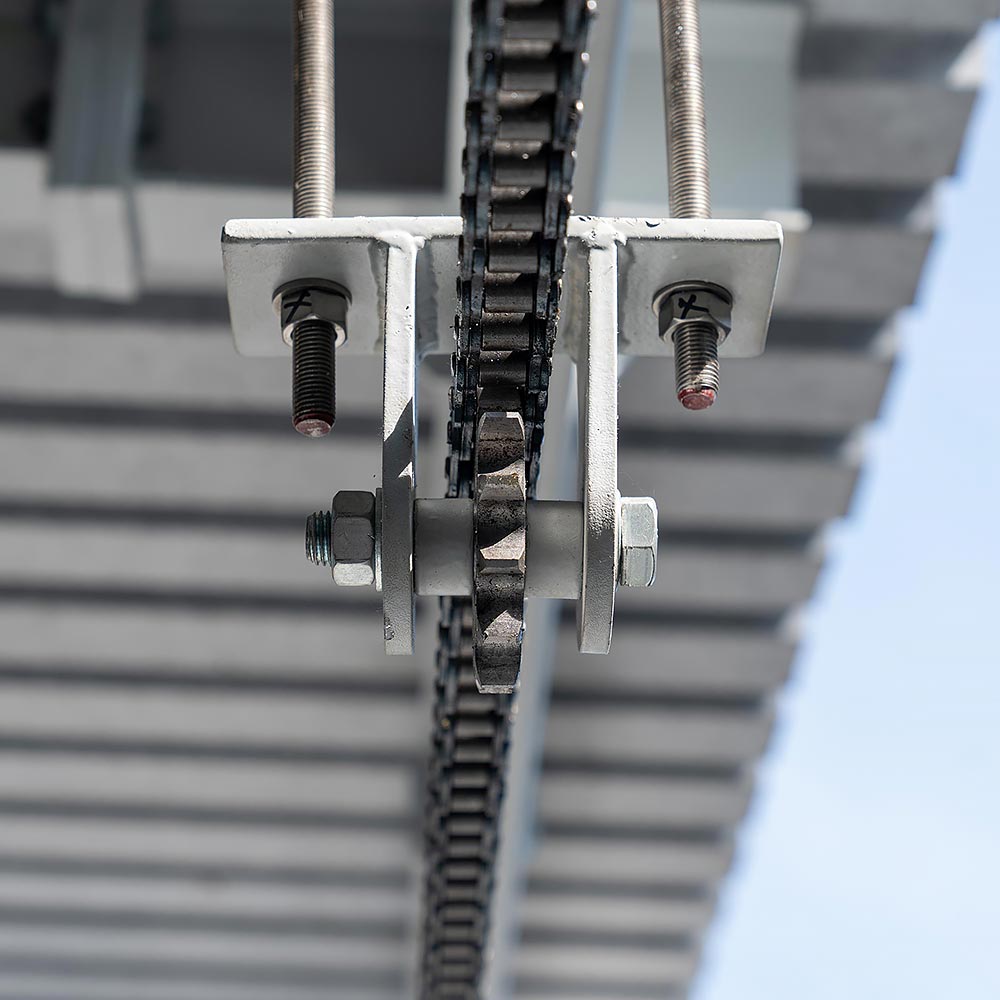
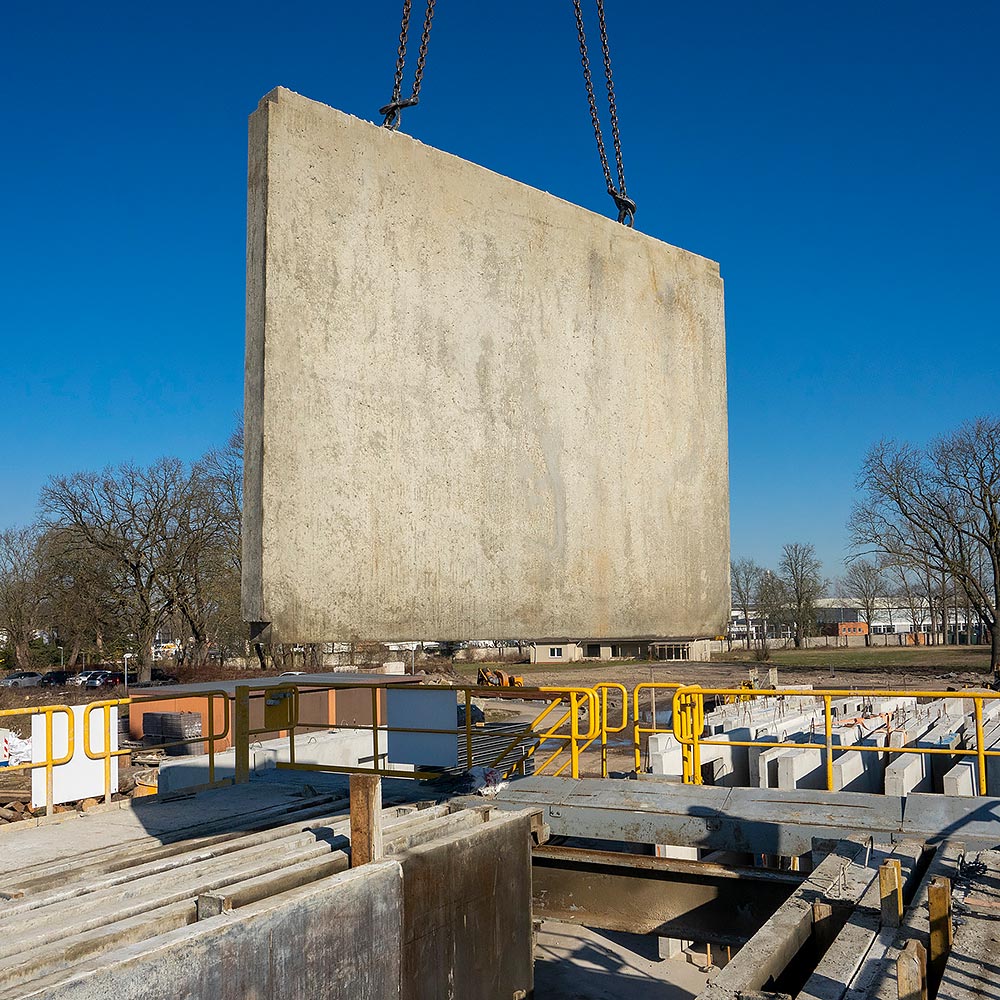
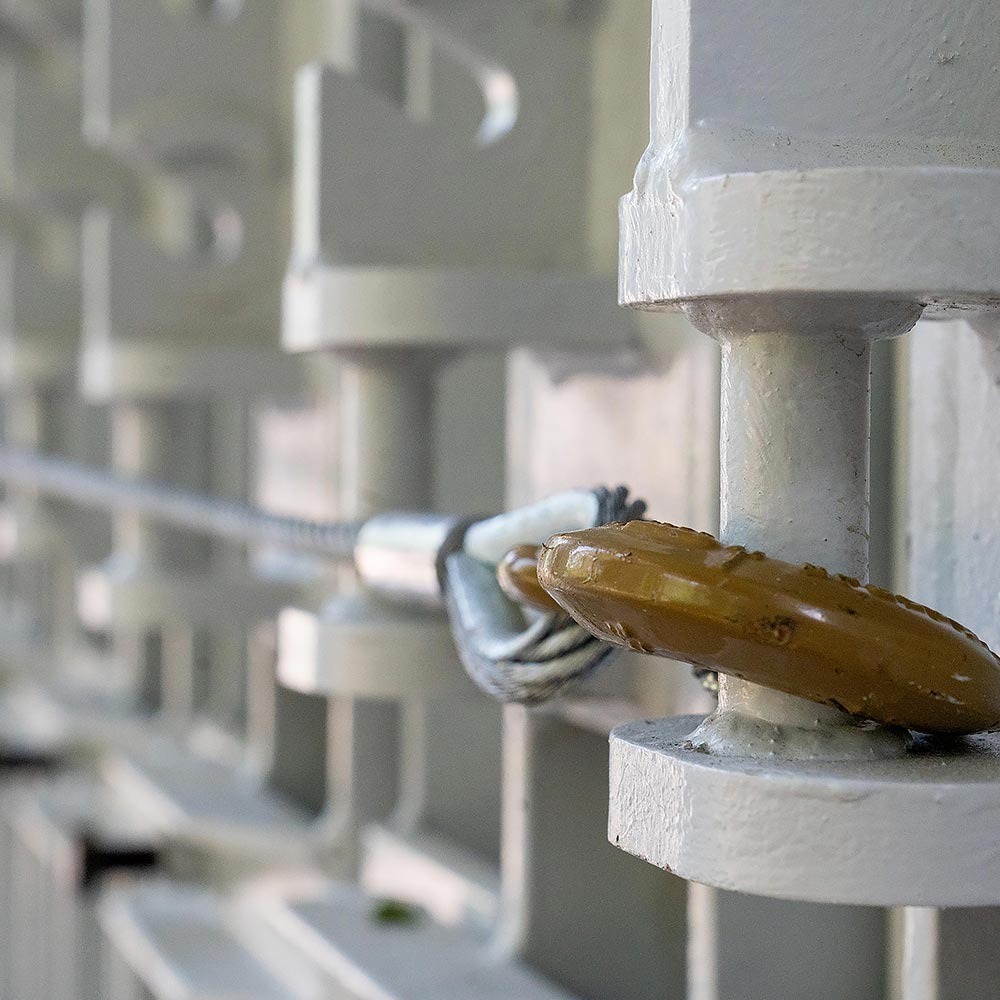
Contact us
Send us a message using the small form below or feel free to call.
Phone
+49 (0)5102 675 4373
Office
Bremer Str. 9 • 30880 Laatzen • Germany
Opening hours
Mo. - Fr. 08:00 - 17:00